Linking onboard units TMS
Tracking & tracing
The planning department tracks the trucks en route via GPRS. The planners see where the trucks are located and where delays are occurring or who is the closest to a particular consignment. Based on real-time information, the planning department adjusts its scheduling. Tracking & tracing is also vital for prompt and accurate information provision to both dispatchers and recipients.
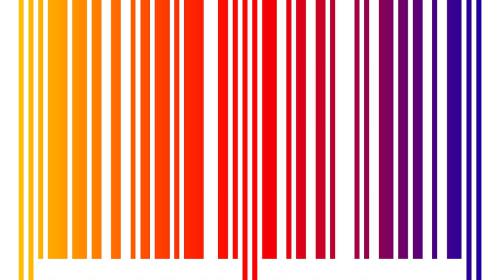
Messaging
Via the GPRS connection between onboard units and the TMS, messages can be exchanged between the planning department and the drivers. The drivers receive new shipment requests on their onboard unit, and the tracing thereof runs (automatically) from the onboard unit back to the planning department. Moreover, information pertaining to goods in, packaging, losses, petrol receipts, working hours and rest periods etc. runs via the onboard unit back to the TMS.
Optimal shipment planning
Via a planning system the driver receives the optimum shipment sequence on their onboard unit. If (for example due to a traffic jam) the navigation system in the truck recognises that the sequence or route changes, then an APS can compute this information and via a link-up with the TMS you can inform the dispatchers and recipients of the amended ETA. The planning department is informed via a message sent by the TMS when a driver deviates from the planned route or when a particular route isn’t proceeding as planned.
App for smartphone or tablet
As standard Dynamics 365 Business Central offers an app for mobile phones and tablets. Our TMS and WMS software is available on this app. So, even without an onboard unit your drivers can register data in the TMS via this app. They can run through various pre-set forms on the app, whereby different processes are provided with data, loading & unloading times, packaging amounts, damage and losses. They can even take a photo and link it directly to a specific file.
Fuel consumption and speed
As the onboard units store data on fuel consumption, speed and lead times that information is also made available in the TMS via the link-up. That data can subsequently be used to optimise business processes and make reports available to management.
Time-keeping
In general onboard units also store the exact driving, loading and unloading and rest periods of a particular driver, and pass these on to a back office system. These hours are often processed in a separate payroll system or in the financial package. With our TMS software you have the option to communicate this data with the payroll software.